Response in a Time of Crisis: How THL Kept Nestlé Waters Moving
A Case Study on Agile Logistics & Crisis Management
The Challenge
A natural disaster disrupted production and halted operations at a critical Nestlé Waters facility.
THL’s Solution
WPL rapidly converted an overflow warehouse into a mixed product distribution center while THL provided the necessary expertise in crisis logistics.
Impact
The initiative not only met but exceeded Nestlé Waters’ inventory accuracy requirements, saving time, reducing expenses, and preventing potential lost sales.
The Challenge
Nestlé Waters, a division of Nestlé, is a leading global provider of bottled water and related products. Its operations are highly dependent on stringent quality and inventory standards to ensure that consumers receive safe, reliable products.
In 2016, a devastating tornado struck Nestlé Waters’ plant in Hawkins, Texas, causing severe damage and an immediate shutdown of operations.
Operational Shutdown: Immediate cessation of production threatened to create a supply gap.
Inventory Risk: Without swift action, there was a risk of significant inventory loss and compromised product quality.
Financial & Reputational Concerns: Delays in distribution could have led to lost sales, increased costs, and diminished consumer trust.
Impact
Contextual Factors
The urgent need to maintain product availability during a natural disaster.
The requirement to quickly adapt existing facilities to handle an expanded product mix.
Ensuring inventory was tracked and maintained to the highest standards during the crisis
Our Solution
Emergency Response Activated
Activated emergency protocols to address the production halt at the Hawkins plant.
Identified and mobilized the overflow warehouse as an alternative distribution hub.
Warehouse Reconfigured
Expanded the operational capacity of the facility, increasing the SKU range from 15 to 135 to meet diverse product needs.
Advanced Inventory Systems Installed
Implemented advanced tracking systems to maintain inventory accuracy that exceeded Nestlé Waters’ standards.
Long-Term Logistics Strategy Developed
THL’s proven capability in crisis management led to the subsequent designation of the WPL facility in Mesquite as an off-site return center for Nestlé Waters, ensuring continued resilience in the Texas region.
The Results
15 → 135
SKU Expansion
near 0%
Operational Downtime
Inventory Accuracy, exceeding Nestlé’s benchmark
99.8%
100%
fulfillment maintained throughout crisis
“The rapid response and precision in inventory management during a crisis were outstanding. Thanks to WPL and THL, we not only maintained our supply chain integrity but also set new standards for crisis response,”
- Operations Executive at Nestlé Waters
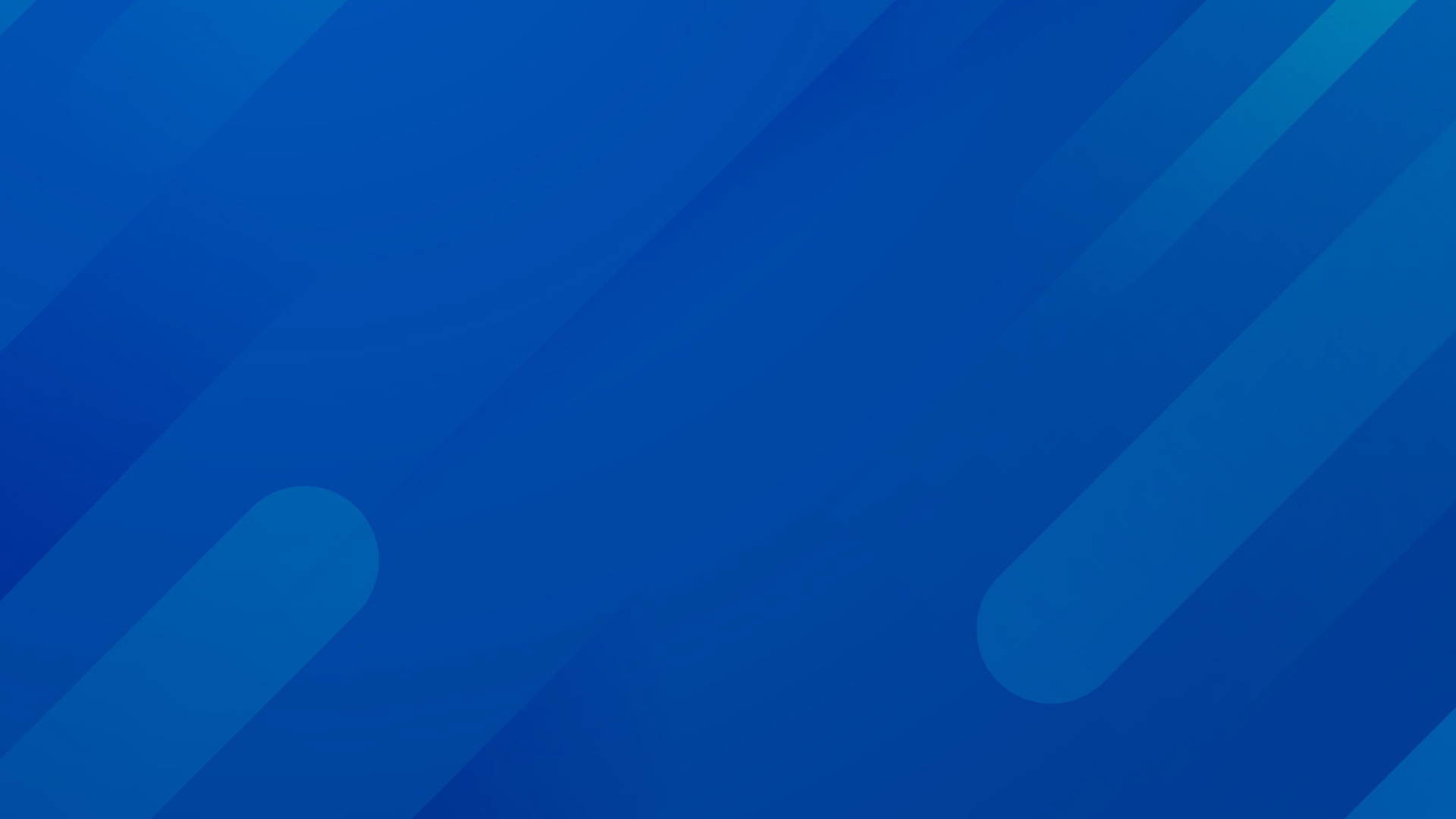
Expertise Applied
Proactive crisis response minimizes operational disruptions.
Expand contingency planning for future supply chain disruptions.
Leveraging existing warehouse infrastructure can be a scalable, cost-effective solution.
Future Considerations
Strengthen off-site warehouse capabilities for emergency response.
Data-driven inventory management ensures continuity even under extreme conditions.
Continue refining rapid deployment protocols to ensure seamless crisis logistics.