Optimizing Supply Chain & Order Fulfillment: How TH Logistics Transformed BHP Marine’s Maxton, NC Operations
The Challenge
Disjointed supply chain systems and delayed order fulfillment were impacting customer satisfaction and operational efficiency.
THL’s Solution
TH Logistics implemented advanced supply chain management technologies, restructured inventory processes, and optimized order fulfillment procedures.
Impact
Significant improvements were achieved, including a 50% reduction in order turnaround time, a 70% decrease in inventory errors, and enhanced customer satisfaction.
The Challenge
Founded in 2003, BHP Marine has long been recognized for its marine services and innovative solutions. However, its Maxton, NC operation was facing challenges with fragmented supply chain processes and inefficient order fulfillment.
TH Logistics was brought on board to revamp these critical areas, modernizing the supply chain and streamlining order processing.
Operational Delays: Extended order turnaround times adversely affected customer satisfaction.
Inventory Mismanagement: Frequent stockouts or overstock situations increased operational costs.
Competitive Disadvantage: Inability to meet modern supply chain standards placed the company at a disadvantage against more agile competitors.
Impact
The growing need for real-time data and efficient inventory tracking in a dynamic market.
Evolving customer expectations for quick, reliable order processing.
The opportunity to leverage technology to streamline supply chain operations.
Contextual Factors
Our Solution
Assessment & Strategy Development
Conducted an in-depth analysis to identify bottlenecks and key areas for improvement in the existing supply chain processes.
Developed a tailored roadmap for restructuring operations.
Technology Integration
Deployed an integrated supply chain management system for real-time inventory tracking and order processing.
Automated key tasks such as reordering and shipment scheduling.
Process Optimization
Reengineered warehouse workflows to reduce manual errors and improve efficiency.
Established standardized protocols for order processing and fulfillment.
Conducted comprehensive training sessions to ensure all team members could effectively utilize the new systems and processes.
Continuous Improvement
Established regular performance reviews and feedback sessions to adjust processes based on real-time data and evolving operational needs.
The Results
50%
reduction in order turnaround time
70%
decrease in inventory discrepancies
Lowered operational costs through automation and improved accuracy
Enhanced customer satisfaction with faster, more reliable service
TH Logistics has revolutionized our order fulfillment process. Our clients are now receiving their orders faster and with greater accuracy,”
- Operations Manager at BHP Marine
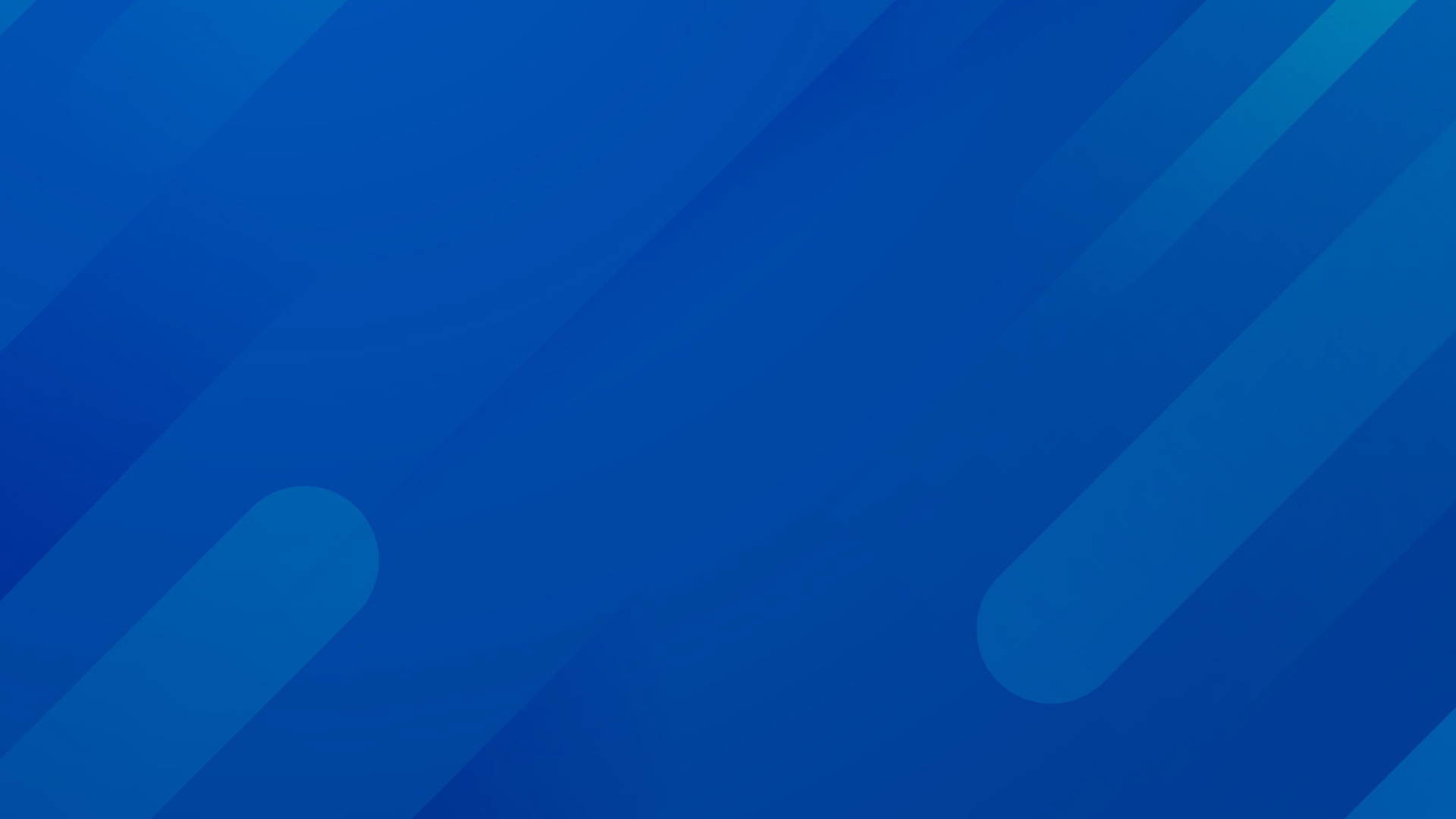
Expertise Applied
Advanced supply chain optimization and process restructuring.
Further invest in predictive analytics to enhance demand forecasting and inventory management.
Implementation of real-time inventory management technology
Future Considerations
Exploring additional automation opportunities may yield further efficiency gains in order fulfillment.
Change management and staff training for seamless system adoption.
Continuously monitor and adjust processes based on performance metrics and employee feedback.